How Does a Diaphragm Pump Work? A Look Behind the Technology
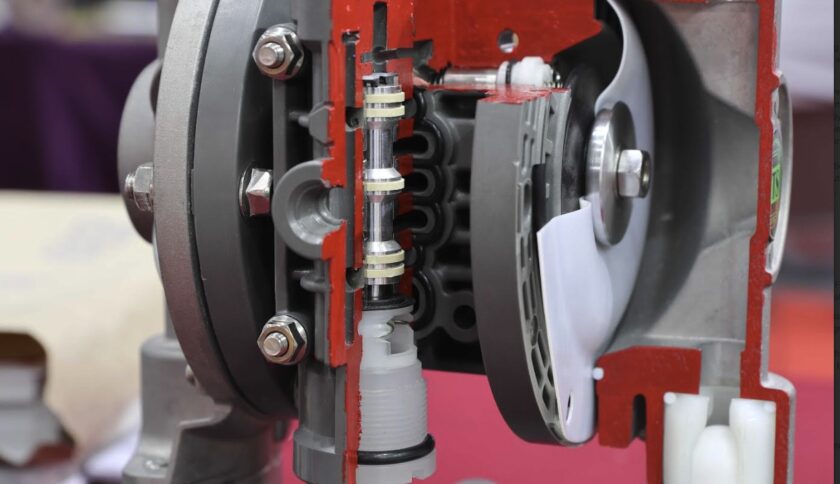
Ever wondered how a diaphragm pump powers through tough jobs like a pro? These unsung heroes quietly handle everything from corrosive chemicals to delicate fluids with precision and reliability. But what’s really going on inside this hardworking pump? Let’s dive into the mechanics and see how it could be the perfect fit for your next project!
What is a Diaphragm Pump?
The diaphragm pump is a positive displacement type of pump where the displacement is achieved through a flexible membrane known as the diaphragm. Through the diaphragm’s back-and-forth motion, it creates the pumping action, sucking liquid or gas into one chamber and pushing it out through another. Simple, yet effective.
These pumps are widely used for handling a wide variety of fluids, including corrosive chemicals, viscous liquids, and even slurries. Due to their sealed design, diaphragm pumps prevent leaks, making them a go-to choice for industries like medical technology, mechanical engineering, and process engineering.
Companies like KNF have perfected the design of diaphragm pumps, offering innovative solutions for handling fluids in applications ranging from laboratory setups to industrial processes.
They are available in various configurations, including electric diaphragm pumps and pneumatic diaphragm pumps, and are highly adaptable for transfer applications. Whether you need precision or power, a diaphragm pump can fit the job, offering reliability and durability in countless setups.
How Does a Diaphragm Pump Work?
The way it works is by drawing in fluid due to the creation of suction cycles with the forward and backward motion of a flexible diaphragm. It can be likened to a heartbeat. When the diaphragm goes back, negative pressure occurs within the chamber, pulling fluid through the check valves. When it goes forward, the fluid gets forced out from the pumping chamber and into the outlet.
There are two main types: electric diaphragm pumps, which use a motor as the power source, and pneumatic diaphragm pumps, which rely on compressed air supply. Both types use similar mechanisms but are suited for different transfer applications.
The process is smooth, efficient, and leak-free, even with challenging materials like corrosive chemicals or viscous fluids. Their robust design and ability to deal with a wide range of fluids makes them a trusted solution across many industries.
Advantages of Diaphragm Pumps
Diaphragm pumps are something that stands out and makes them a favorite for sectors like medical technology, process engineering, and many more. They are quite versatile in that they can handle all kinds of fluids, from the thinnest liquids to viscous slurries and even abrasives or corrosives.
Another plus is their leak-free operation, thanks to the sealed pump chamber and flexible diaphragms; they are suitable for sensitive or hazardous fluids. They also happen to be self-priming and are thus able to start pumping even if not completely filled with liquid-very handy for many transfer applications.
Durability is a feature that stands out, such as reinforced membranes that can withstand demanding conditions. Diaphragm pumps are also low maintenance, reducing downtime and costs. Whether you need precision or power, these pumps deliver consistent performance, making them a reliable choice across countless industries.
Applications of Diaphragm Pumps
Diaphragm pumps can be used in any industry. For example, they are commonly found in devices that require the accuracy and zero-leak capability that medical technology needs, such as dialysis machines and laboratory equipment.
Diaphragm pumps are excellent for transferring corrosive chemicals, viscous fluids, or even slurries in mechanical and process engineering. They are widely used in water treatment, chemical dosing, and transferring fuels or oils. Their ability to handle sensitive fluids without contamination also makes them ideal for the food and beverage industry.
For laboratories, diaphragm pumps excel in filtration systems and fluid handling tasks, where accuracy and cleanliness matter most. Their versatility across industries, coupled with a robust and low-maintenance design, makes them the go-to solution for demanding pumping tasks in thousands of applications. No matter the task, diaphragm pumps do it, especially when paired with other technologies like medical air systems.
Possible Limitations and Considerations
It may be noted that diaphragm pumps are versatile and reliable but are not without a few limitations. Key consideration for all diaphragm pumps is noise: pneumatic diaphragm pumps especially tend to be somewhat very loud because of the use of compressed air. For noise-sensitive environments, electric diaphragm pumps may suit better.
Efficiency can also differ; diaphragm pumps will have a relatively lower flow rate for certain applications with high volume compared to other types of pumps. Proper installation and maintenance are also essential to prevent problems such as air leaks or wear on the flexible diaphragms.
The pump material compatibility may also be involved; the wrong diaphragm material for corrosive or abrasive fluids can cause the pump’s lifespan to reduce. For effective performance, choose the right design of the pump, the suitable material for the diaphragm, and the proper power source in accordance with your needs. Planning a little step will ensure the pump works harmoniously.
Your Next Step to Pumping Success
Diaphragm pumps are reliable, versatile solutions for complex fluid-handling needs. Their efficiency and durability make them a smart choice across industries. Ready to tackle your toughest pumping challenges? Explore diaphragm pump options today and discover how they can simplify your processes while boosting performance. Your perfect pump is waiting!
Spotted something? Got a story? Send a Facebook Message | A direct message on Twitter | Email: [email protected] Latest News