5 Important Things Not to Do in Installing Globe Valves
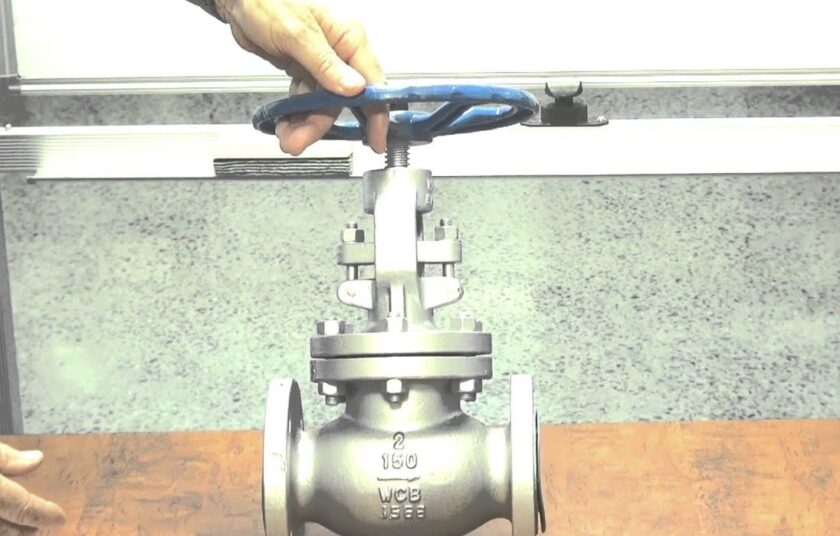
Installing a globe valve might seem straightforward, but even small mistakes can lead to leaks, pressure issues, or system failures.
To ensure your globe valves function properly, it’s important to know what not to do during installation.
This guide will highlight five key mistakes to avoid so you can set up your system correctly and prevent costly repairs down the line.
1. Ignoring Flow Direction Markings
In order to indicate the appropriate flow direction, globe valves are equipped with arrows or markings. As a result of ignoring these, the valve may experience poor performance and even be damaged.
When the valve is installed in the wrong direction, it may not be able to control flow effectively, which can result in pressure buildup or leaks.
Prior to installation, you should always check the markings. If unsure, refer to the manufacturer’s guide. Installing the valve correctly ensures smooth operation and prevents costly repairs.
2. Over-Tightening the Valve
Connections that are overly tightened can cause the valve body to crack or the sealing parts to deform, which subsequently renders the valve ineffective.
To prevent these issues from occurring, make sure to secure the valve with the recommended amount of torque. If you notice leaks, rather than trying to force the valve to be tighter, you should check for proper sealing.
Having a valve that is properly tightened will make it last longer and will function more effectively.
3. Skipping Proper Alignment
In the event that the valve is not properly aligned with the pipeline, it has the potential to induce stress on the connections, which in turn can result in leaks. Misalignment can also make the valve difficult to operate or reduce its lifespan.
Before beginning the installation process, check that the valve and the pipeline are all perfectly aligned. When you want to keep everything in place, use the appropriate support. Taking time to align the valve correctly helps prevent long-term issues.
4. Using the Wrong Valve Size
If a globe valve is to function properly, it must be the same size as the pipe. Using a valve that is too big or too small can restrict flow, create pressure problems, or cause inefficiencies.
Always make sure to check the specifications of the valves and measure them against the size of the pipeline. Installing the right-sized valve improves performance, prevents damage, and ensures smooth flow control.
5. Neglecting to Clean the Pipeline Before Installation
Dirt, debris, or leftover materials inside the pipeline can clog the valve and cause it to malfunction. Before installing a globe valve, always flush the pipeline to remove any foreign particles. A clean pipeline helps prevent blockages, reduces wear on the valve, and ensures smooth operation. Taking this step avoids performance issues and extends the valve’s lifespan.
Have Safer and More Reliable Valve Function
Proper installation is key to ensuring the efficiency and longevity of globe valves. Take the time to follow best practices, and you’ll enjoy a safer and more durable valve system.
Spotted something? Got a story? Send a Facebook Message | A direct message on Twitter | Email: [email protected] Latest News